Early practical application of low-cost and energy-saving CO2 separation/capture technology will contribute to realizing a carbon neutral society
Showa Denko K.K. (President: Hidehito Takahashi, hereafter referred to as SDK), Nippon Steel Corporation (President: Eiji Hashimoto, hereafter referred to as NSC), and six national universities (Oita University, Osaka University, Kyoto University, Chiba University, Nagoya University, and Hokkaido University) have jointly formed a technology development project (hereafter referred to as this Project). Granted as one of the Green Innovation Fund Projects under the New Energy and Industrial Technology Development Organization (NEDO), this Project ramped up development activities in October 2022. This project aims to separate/ capture CO2 efficiently from low pressure/low-concentration (atmospheric pressure; CO2 concentration: 10% or lower) discharge gas by using the technologies owned by these two companies and six universities. With the target of achieving an innovatively low cost of 2,000-yen level per ton, this technology is slated for social implementation in the late 2030s. Furthermore, SDK aims to establish a business model that reuses/sells captured CO2 as raw materials of chemical products.
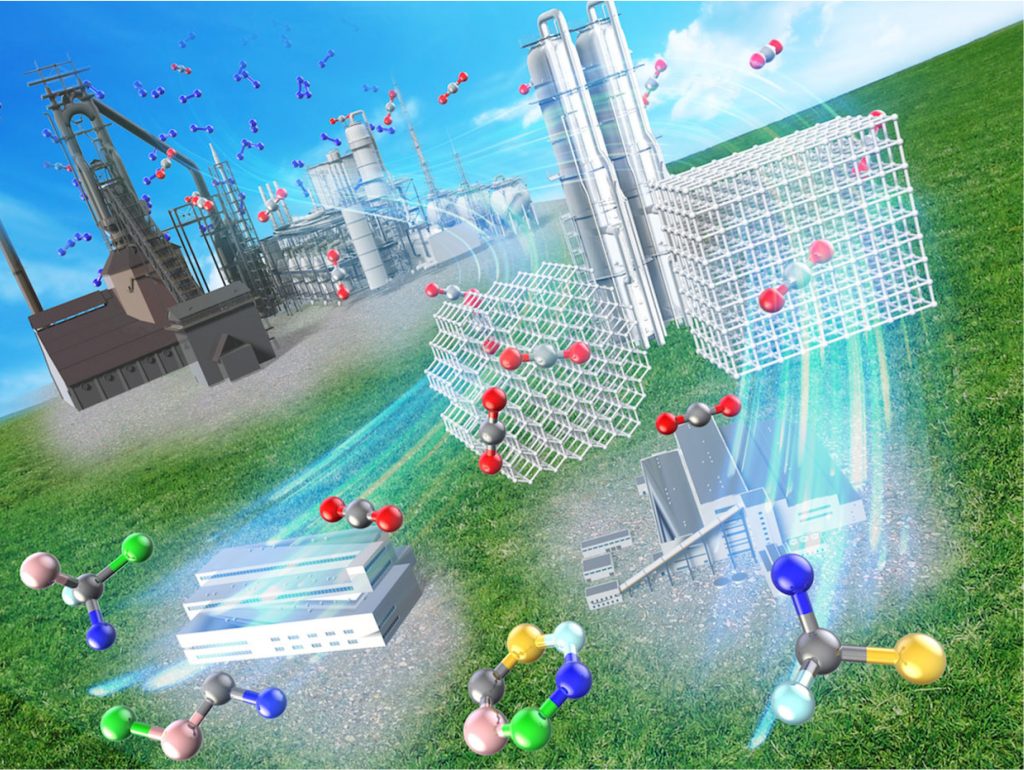
The period of this Project’s R&D activities is nine years from fiscal 2022 to fiscal 2030. Its budget is approx. 8.4 billion yen in total.
Compared with high-pressure gas with a high-concentration of CO2 discharged from coal fired power generation plants or similar facilities, low-pressure gas with a low-concentration of CO2 (atmospheric pressure; CO2 concentration: 10% or lower) discharged from plants such as those in a petrochemical complex or steel mills has big issues such as: (1) separating CO2 selectively is difficult, and (2) separating processes consume huge amounts of energy. For these reasons, social implementation of CO2 separation/capture technology has not seen much progress.
This Project has a new challenging development plan that will resolve the issue described above fundamentally by applying a structurally flexible PCP*3, which is totally different from conventional porous materials (such as zeolite and activated carbon), to the process of CO2 separation/capture from discharge gas with a low pressure and a low concentration of CO2. While gas molecules are trapped in rigid nano-level pores of zeolite, for structurally flexible PCP, the structure flexibly changes to take in CO2 molecules to form complexes (inclusion complexes). Its high selectivity for CO2 is expected to be effective, because only CO2 molecules, which help form complexes stably, are captured.
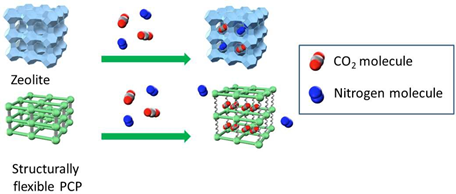
For conventional porous materials, as the green line in Figure 2 shows, the CO2 adsorption amount increases and decreases monotonically with respect to the CO2 pressure. In this case, in order to capture CO2 adsorbed at a high pressure (point A), the pressure has to be decreased all the way to a low pressure (point B) with a machine such as a vacuum pump. These compression and depression operations consume large energy. On the other hand, for the material to be developed by this Project, as the blue line in Figure 3 shows, the CO2 adsorption amount changes sharply at a specific pressure. This peculiar behavior is called gate adsorption. When gate adsorption is used, changing pressure slightly between points C and D can advance CO2 adsorption and desorption. Compared with conventional materials such as zeolite, this material of gate adsorption can reduce theoretically the consumption energy significantly for separation/capture of CO2.

Figure 3 (Right): Adsorption characteristics of structurally flexible PCP
In order to achieve social implementation of the innovative CO2 separation technology using this new material, SDK and NSC will combine the separating agent technologies each has originally developed to develop a new revolutionary separating agent that separates CO2 from discharge gas with a low concentration of CO2 and that is characterized by low cost and low energy consumption during the separation process. In addition, through the co-creation process of the joint development with Oita University, Osaka University, Kyoto University, Chiba University, Nagoya University, and Hokkaido University, this Project aims at achieving these goals as early as possible.
[Specific activities]
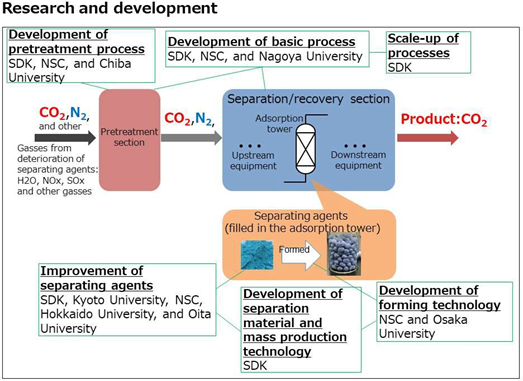
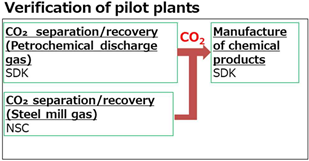
- Improvement of separation agent (SDK, NSC, Oita University, Kyoto University, and Hokkaido University)
Improve the characteristics of separation agents (adsorption pressure and amount). - Process development
- (2)-1 Studying forming technology (NSC and Graduate School of Engineering, Osaka University) Develop a method for forming the separating agent into optimum shapes (development of formative technology)
- (2)-2 Gas pretreatment process development(SDK, NSC, and Chiba University)
Each company will develop/design separately the process of removing impurities that promote separating agent deterioration to separate CO2 efficiently because components contained in gas vary depending on emission sources. - (2)-3 Basic process development (SDK, NSC, and Nagoya University)
Optimize the processes (shapes of machines and operation conditions) that matches the special CO2 separation behavior (gate adsorption behavior) of the structurally flexible PCP. - (2)-4 Scale-up of processes (SDK)
Based on the laboratory level basic processes, study the scale-up of processes and design a pilot plant (machines and operation conditions). - Development of separating agent mass production technology (SDK)
Study mass production technology for manufacturing several tens to several hundreds of tons of separating agent (PCP powder and its formed bodies) in the future. - Construction and verification of the pilot plants for CO2 separation (SDK and NSC)
Verification using petrochemical discharge gas will be conducted at SDK Oita Complex, and verification using discharge gas of steel mills at Oita Area, Kyushu Works, NSC. Both companies will verify the productivities, selectivities, capture rates, lives of separating agents and product qualities, and assess the economic efficiencies of the preprocesses and separating processes. - Verification of the pilot plant of manufacturing chemical products (SDK)
A pilot plant will be constructed at SDK Oita Complex to manufacture chemical products using CO2 captured from petrochemical and steel mill discharge gas each as a raw material, and verification of manufacturing chemical products using actual gas and assessment of economic efficiency of the plant will be carried out.
[Schedule]

*1: The formal title of the project is “Development of low-concentration CO2 separation system using an innovative separating agent/Technology development and demonstration of small- and medium- scale CO2 separation and capture from factory exhaust gas, etc.” It was adopted in May 2022.
*2: The formal title: “Development of Technology for CO2 Separation, Capture, etc./Green Innovation Fund Projects”
*3: PCP abbreviation stands for Porous Coordination Polymer.
Contact information for inquiry about this material
Showa Denko K.K.:
Public Relations Group, Brand Communication Department
Tel: +81-3-5470-3235
Nippon Steel Corporation:
Public Relations Center, General Administration Div.
Tel: +81-3-6867-2977
Oita University:
Public Relations Unit, General Affairs Division, Department of General Affairs
Tel: +81 -97 -554 -7376
Osaka University:
Assessment and Publicity Section, General Affairs Division, Graduate School of Engineering
Tel: +81-6-6879-7231
Email: kou-soumu-hyoukakouhou@office.osaka-u.ac.jp
Kyoto University:
iCeMS Communication Design Unit
Tel: +81-75-753-9749
Email: cd@mail2.adm.kyoto-u.ac.jp
Chiba University:
Public Relations Office
Tel: +81-43-290-2018
Nagoya University:
International Communications Office
Tel: +81-52-747-6862
Email: kouho-en@adm.nagoya-u.ac.jp
Hokkaido University:
Shin-ichiro Noro, Professor, Graduate School Faculty of Environmental Earth Science
Tel: +81-11-706-2272
Email: noro@ees.hokudai.ac.jp
Public Relations Division, Department of Public Engagement, Hokkaido University
Tel: +81-11-706-2610
Email: en-press@general.hokudai.ac.jp
Recommend
-
Creating a Flourishing Society with Novel Cultivars of Fruits: Integrating Molecular Genetics, Statistical Genetics, and Data Science for Efficient Fruit Tree Breeding
2023.09.08
-
The Science Behind Nature’s Touch: Horticultural Therapy and Community Well-Being
2025.01.14
-
The Global Goal of Carbon Neutrality by 2050 (Part 1): Universities as Agents of Change
2023.07.12